Fugitive emissions
Emissions below 10 ppmV in API 622 testing
Equipment leaks from valve glands are considered to account for approximately 50-60 % of the fugitive emissions on petrochemical sites. Furthermore, the major proportion of fugitive emissions comes from only a small fraction of the sources. For example, less than 5 % of valves in gas/vapour service can account for more than 90 % of the fugitive emissions in a refinery.
James Walker® has developed products specifically to combat fugitive VOC emissions from valves, including Supagraf® Premier, Supagraf® Control, and Supagraf® FE. These products have proven themselves to be class-leaders in a series of third party fugitive emissions performance tests are best available technique (BAT) products for reducing industry’s fugitive emissions in line with the latest Industrial Emissions Directive. James Walker® fugitive emission control packings have been tested and delivered proven performance to the most exacting industry standards and end-user requirements:
- API 622
- ISO 15848-1 Class AH CO3
- ISO 15848-1 Class BH CO3
- TA Luft Rev07.2002
- Shell Spec SPE 77/312 Class A
- Shell Spec SPE 77/312 Class B
- API 607 Edition 4 fire safety
- Shell MESC SPE 85/204
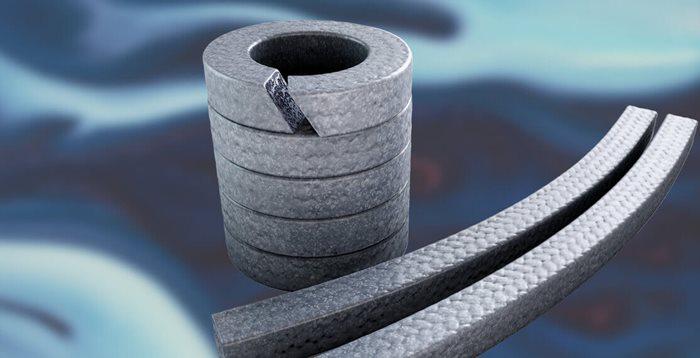
A longterm, high integrity sealing solution for control valves.
Supagraf® Control is an innovative compression packing that provides long-term, high integrity sealing for control valves. Its very low friction enhances the control accuracy of valves. This is a ‘best available technique’ product for reducing industry’s VOC fugitive emissions in line with the European Union’s IPPC Directive.
It is manufactured in exfoliated graphite, reinforced in a novel way with a non-metallic structure to provide additional strength and resistance to pressure and extrusion. An advanced lubricant system is incorporated to prevent the pick-up of graphite on valve stems.
Product features
- High integrity gland sealing for control valve stems: to well below 50 ppm fugitive emission level
- Long-term adjustment-free operation: over 100,000 stem strokes with emission levels below 50 ppmV
- Very low coefficient of friction for smooth and accurate valve action
- Reduced friction requirement to save on power consumption and enable smaller actuators to be used
Designed for emission control – to better than 50 ppmV leak tightness – on control valves in systems handling fluid media such as hydrocarbon liquid fuels and gases, lubricating oils and hazardous process chemicals
It is a long-term replacement for the PTFE V-type packings that can be readily damaged by ingress of dirt and other foreign particles to the gland area
Valve stem duties:
- Maximum operating temperature: Up to + 350 °C (+ 662 °F)
- Minimum operating temperature: – 200 °C (- 328 °F)
- Maximum system pressure (standard): 25 MPa / 250 bar (3626 psi) – contact us for advice on use at higher pressures
Chemical properties
Compatible with media in the range of pH 1-14 excluding strong oxidising agents. The product has low volatile content.
- All popular square sections from 3 mm (1/8“) upwards in boxes containing 8 m (26′ 3”) in coil form or on spools as detailed in the product datasheet
- Also supplied as split preformed rings and sets
- Non-standard square or rectangular sections made to order
- Please refer to the product datasheet for spool ordering information
Approvals & certifications
- TA Luft/VDI 2440
- ISO 15848-1 Class BH, CC3
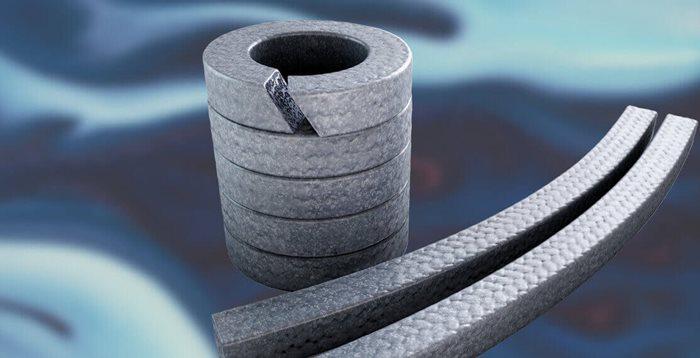
A high performance fugitive emission control packing for valves.
Supagraf® FE is third party tested to all known industry standards producing exceptional performance, 8 ppmV average emission level in API 622 3rd edition test with no adjustments. This is a cost effective fully braided packing manufactured in exfoliated high purity 98 % graphite, reinforced with Inconel wire to provide additional strength and resistance to pressure and extrusion.
This packing incorporates a new generation cutting-edge lubrication system that not only helps to prevent the pick-up of graphite on valve stems but also provides ultra-low friction performance with advanced corrosion inhibiting properties.
Product features
- Third party verified emission control performance
- Suitable for both rotary as well as rising-stem valve application
- Ultra-low friction performance without graphite pick-up reducing the torque needed for efficient valve action
- Fire safe capability confirmed by third-party certification according to API 607 Edition 7 Fire Safety / ISO 10497:2010
- Suitable for use in valves from pressure Class 150 up to Class 1500 – please consult us for further advice and Class 2500 suitability
- Can mitigate the effects of stem judder and friction by helping to prevent graphite pickup or high spot friction on the valve stem, especially in applications with high rates of thermal cycling and dynamic stem movements
- Supagraf® FE is designed for harsh operating conditions where fugitive emissions from valves need to be reduced to well below 50 ppm
- Suitable for all types of valves performing arduous duties handling fluid media such as hydrocarbon liquid fuels and gases, lubricating oils and processing chemicals
- Also suitable for valves that handle dry gases and other fluids
Valve stem duties:
- Maximum operating temperature in oxidising conditions: + 450 °C (+ 842 °F)
- Minimum operating temperature: – 200 °C (- 328 °F)
- Maximum system pressure (standard): 25 MPa / 250 bar (3626 psi) – contact us for advice on use at higher pressures
Chemical properties
Compatible with media in the range of pH 1-14 excluding strong oxidising agents. The product has negligible volatile content.
- All popular square sections from 3 mm (1/8“) upwards in boxes containing 8 m (26′ 3”) in coil form or on spools as detailed in the product datasheet
- Also supplied as split preformed rings and sets
- Non-standard square or rectangular sections made to order
- Please refer to the product datasheet for spool ordering information
Approvals & certifications
- ISO 15848-1:2015 Class BH (CO1)
- API 622 3rd Edition
- TA Luft VDI 2440 Rev. 07.2002
- Shell MESC SPE 85/204
- Shell specification SPE 77/312 Class AH Rev. 02.2019
- API 607 Edition 7 Fire Safety
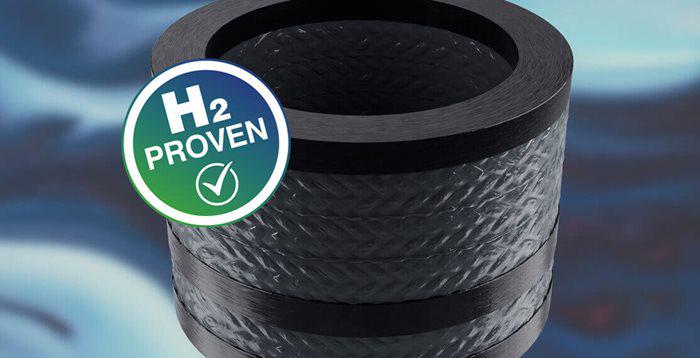
Supagraf® H2 is a high performance, unique combination, valve stem packing set designed for hydrogen service.
This packing solution incorporates Supagraf® Premier, one of James Walker®’s top-of-the-range fugitive emission control packings that has a long track record of exceptional performance in valves handling hydrocarbon liquid fuels and gases, lubricating oils or processing chemicals including hydrogen.
The performance of Supagraf® Premier graphite packing rings are then enhanced by the use of precision machined carbon rings, inserted at the top and bottom of the stuffing box set and used as intermediary rings.
This product has been third party tested and is validated by James Walker® for use in hydrogen service.
Typical applications
Supagraf® H2 is designed specifically for the harsh operating conditions of all types of valves in hydrogen service where exceptional tightness, safety and extended dynamic sealing performance is required.
The product is also compatible with different blends of hydrogen and other liquid or gaseous media as well as hydrocarbons or chemicals.
Performance
Valve stem duties
- Maximum operating temperature in oxidising conditions: + 450°C (+ 842°F)
- Minimum Operating Temperature: – 253 °C (- 423 °F)
- Maximum System Pressure (Standard): 69 MPa / 690 bar (10000 psi)
Contact us for advice where operating conditions are outside these limits.
Chemical properties
Compatible with media in the range of pH 0-14 excluding strong oxidising agents. The product has negligible volatile content.
How supplied
As preformed graphite rings with a single split combined with precision machined carbon rings supplied endless or split in two matched halves with cut of 45 degrees. Product made to order to suit application requirements.
Approvals & certifications
Supagraf® H2 combination packing set has been 3rd party tested and certified for hydrogen service. The test regime has been adapted from ISO 15848-1 standard and modified with the use of 99 % hydrogen test media as opposed to ISO 15848-1 specified helium gas. The product has been tested at room temperature and to CO1 endurance class reaching class BH* leakage performance (with no adjustment).
The product has also been tested according to ISO 15848-1 standard (with helium test media) in configuration of Supagraf® Premier graphite rings with single bottom stuffing box machined carbon ring, achieving class BH tightness at CO1 endurance class and temperature range from – 196 °C [- 321 °F] up to + 400 °C [752 °F] (with no adjustment).
In addition, the stand-alone Supagraf® Premier packing set has been tested and certified to:
- ISO 15848-1 Class AH (fugitive emissions): Certified by ITIS BV at 69 MPa (static) with a five-ring set in a BSM valve. Emission level at 69 MPa / 690 bar (10,000 psi) was ≤ 5 ppmV
- API 622: average emission level of 10.5 ppmV, with a maximum of 37 ppmV over five thermal cycles and 1510 mechanical cycles
- TA Luft Rev 07.2002 requirements/VDI 2440
- Shell specification SPE 77/312 Class A, Rev 16.10.2002
- Shell specification SPE 77/312 Rev 06.2007: Class B rating with 47.4 MPa / 474 bar (6875 psi) helium in Class 2500 valve
- API 607 Edition 4 Fire Safety
- Base graphite material complies to Shell MESC SPE 85/204.
*Note: BH volumetric leak rate used for Hydrogen gas.
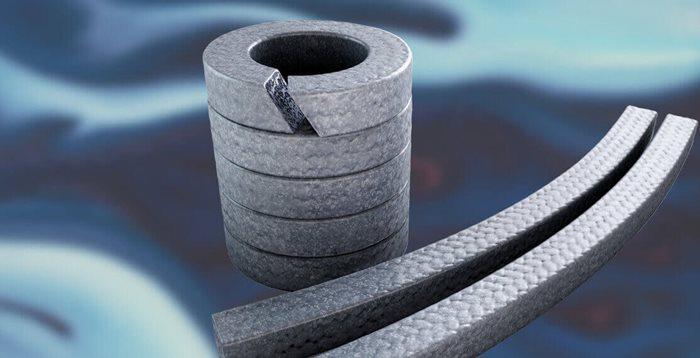
Our world beating fugitive emission control packing for valves, third party tested to all known industry standards.
Supagraf® Premier is manufactured in exfoliated high purity 98 % graphite, reinforced in a novel way to provide additional strength and resistance to pressure and extrusion. It incorporates an advanced lubricant system that prevents the pick-up of graphite on valve stems and produces exceptional performance, 10.5 ppmV average emission level in API 622 2nd edition test with no adjustments.
Product features
- Third party verified emission control performance
- Suitable for both rotary as well as rising-stem applications
- Low friction performance without graphite pick-up reducing the torque needed for efficient valve action
- Fire safe capability confirmed by third-party certification according to API 607 Edition 4 Fire Safety
Typical applications
Supagraf® Premier is designed for harsh operating conditions where fugitive emissions from all types of valves need to be reduced to well below 50 ppm. This packing is well proven and widely used in systems handling fluid media such as hydrocarbon liquid fuels and gases, lubricating oils and processing chemicals.
Performance
Valve stem sealing duties:
- Maximum operating temperature in oxidising conditions: + 450 °C (+ 842 °F)
- Minimum operating temperature: – 200 °C (- 328 °F)
- Maximum system pressure: 25 MPa / 250 bar (3626 psi) – consult us for advice on use at higher pressures
- Certified pressure in BSM valve: 69 MPa / 690 bar (10000 psi)
How supplied
- All popular square sections from 3 mm (1/8“) upwards in boxes containing 8 m (26′ 3”), in coil form or on spools as detailed in the product datasheet
- Also supplied as split preformed rings and sets
- Non-standard square or rectangular sections made to order
- Please refer to the product datasheet for spool ordering information
Approvals & certifications
- ISO 15848-1 Class AH
- API 622 2nd Edition
- TA Luft / VDI 2440 Rev. 07.2002
- Shell MESC SPE 85/204
- Shell specification SPE 77/312 Class A
- Shell specification SPE 77/312 Class B
- API 607 Edition 4 Fire Safety
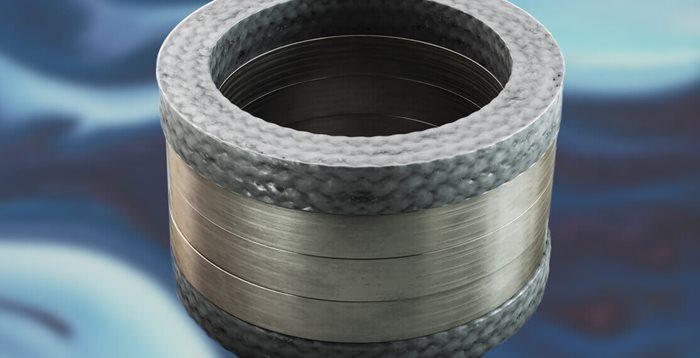
A superior combination packing set for valves based on two classleading graphite products.
Supagraf® Premipak is a superior combination packing set for valves. It is based on two class-leading graphite products.
End rings: Supagraf® Premier braided high purity 98 % graphite filament packing for high strength and extrusion resistance with excellent sealability, plus third-party certification to TA Luft, API 622 or ISO 15848-1 emission control requirements. These rings conform to Shell material specification MESC SPE 85/204.
Intermediate rings: Special moulded rings of high purity graphite foil, that offer low friction and excellent heat transfer characteristics, plus high efficiency sealing. These rings conform to Shell material specification MESC SPE 85/203.
Product features
- Reduced valve stem shudder and hesitation
- Low break-out friction
- Long working life with minimal maintenance
Typical applications
- Stop valves and control valves performing arduous duties with media such as hydrocarbon liquid fuels and gases
- Most applications require VOC fugitive emission control to 100 ppm or better, with a maximum working temperature of up to + 450 °C (+ 842 °F)
Performance
Valve stem duties
- Maximum operating temperature: + 450 °C (+ 842 °F)
- Minimum operating temperature: – 200 °C (- 328 °F)
- Maximum system pressure: 25 MPa / 250 bar (3626 psi)
Chemical properties
Compatible with media in the range of pH 1-14 excluding strong oxidising agents.
How supplied
- As precision moulded rings in endless form or with single split, to meet customers’ requirements
- Sections: 3 mm to 40 mm (1/8” to 19/16“). Diameters: 5 mm to 500 mm (3/16” to 19 3/4“) ID
Approvals & certifications
- Shell MESC SPE 85/203
- Shell MESC SPE 85/204